Material Handling Solutions
Warehouses and distribution centers are under more pressure than ever to move more products with fewer people. Many now run seven days a week just to keep up, which often leads to burnout, bottlenecks, and higher costs. We take a different approach to warehouse automation systems. Instead of jumping straight to robots and conveyors, we start by learning how your operation really works—how materials move, where the pain points are, and what’s holding you back.
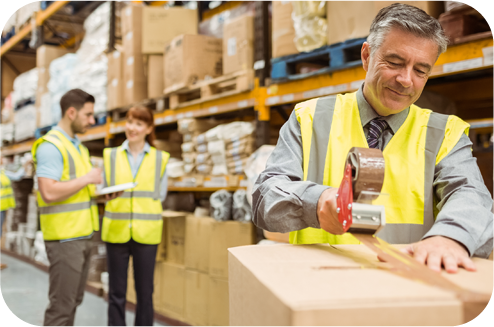
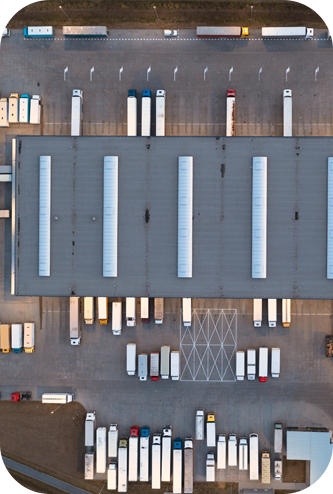
Common Material Handling Challenges
Modern distribution centers face challenges that off-the-shelf solutions weren’t designed to address:
- Chronic labor shortages in critical picking and packing roles
- Increasingly complex order profiles with smaller, more frequent shipments
- Accuracy issues that damage customer relationships and increase returns
- Seasonal fluctuations requiring rapid scaling up and down
- Growing SKU counts that challenge traditional storage systems
- Rising customer expectations for speed and order accuracy
Our Engineering-First Approach to Material Handling Efficiency
Most integrators approach warehouse projects with predetermined equipment packages they’re eager to sell. We start by analyzing your actual material flow patterns and identifying constraints before proposing any solutions. This material handling efficiency approach often reveals that your most pressing challenges can be solved without the massive capital expenditure another vendor might recommend. Our Solution Success Team works independently from our engineering department, ensuring you get unbiased recommendations rather than a sales pitch for equipment.
Solving Real Problems Instead of Just Adding Technology
Many distribution centers don’t need a complete warehouse overhaul to see dramatic improvements. Our targeted approach delivers results through:
- Redesigning picking paths to minimize travel distance and time
- Implementing zone-based fulfillment strategies that maximize productivity
- Creating intelligent slotting systems based on actual order patterns
- Developing custom solutions for unique product handling challenges
- Optimizing existing equipment rather than replacing it unnecessarily
- Establishing data-driven metrics that highlight actual performance
Creating Visibility Through Data Integration
Distribution center optimization starts with understanding what’s really happening on the warehouse floor. Many teams struggle simply because they don’t have a clear view of how things are actually performing. Our approach includes:
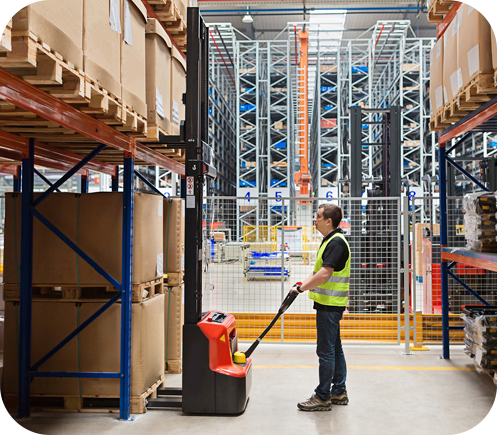
Automated Storage Retrieval Systems That Make Business Sense
Automated storage and retrieval systems (ASRS) can transform distribution operations when implemented correctly. MOT’s engineering team evaluates these technologies based on your specific requirements rather than generic industry standards. Whether you need a solution for small parts management, full-case handling, or oversized product storage, we design systems that address your unique challenges while providing a clear path to ROI. This methodology ensures your warehouse process improvement initiatives deliver measurable business outcomes.
Master the Mess: Take Control of Warehouse Operation
Whether you’re dealing with a completely manual operation that needs modernization or looking to optimize an existing automated system, we’ll develop solutions that address your specific challenges. Contact MOT today to discuss how our holistic approach can provide the material handling solutions you need to stay competitive.